Unveiling the Plunger Pump Working Principle
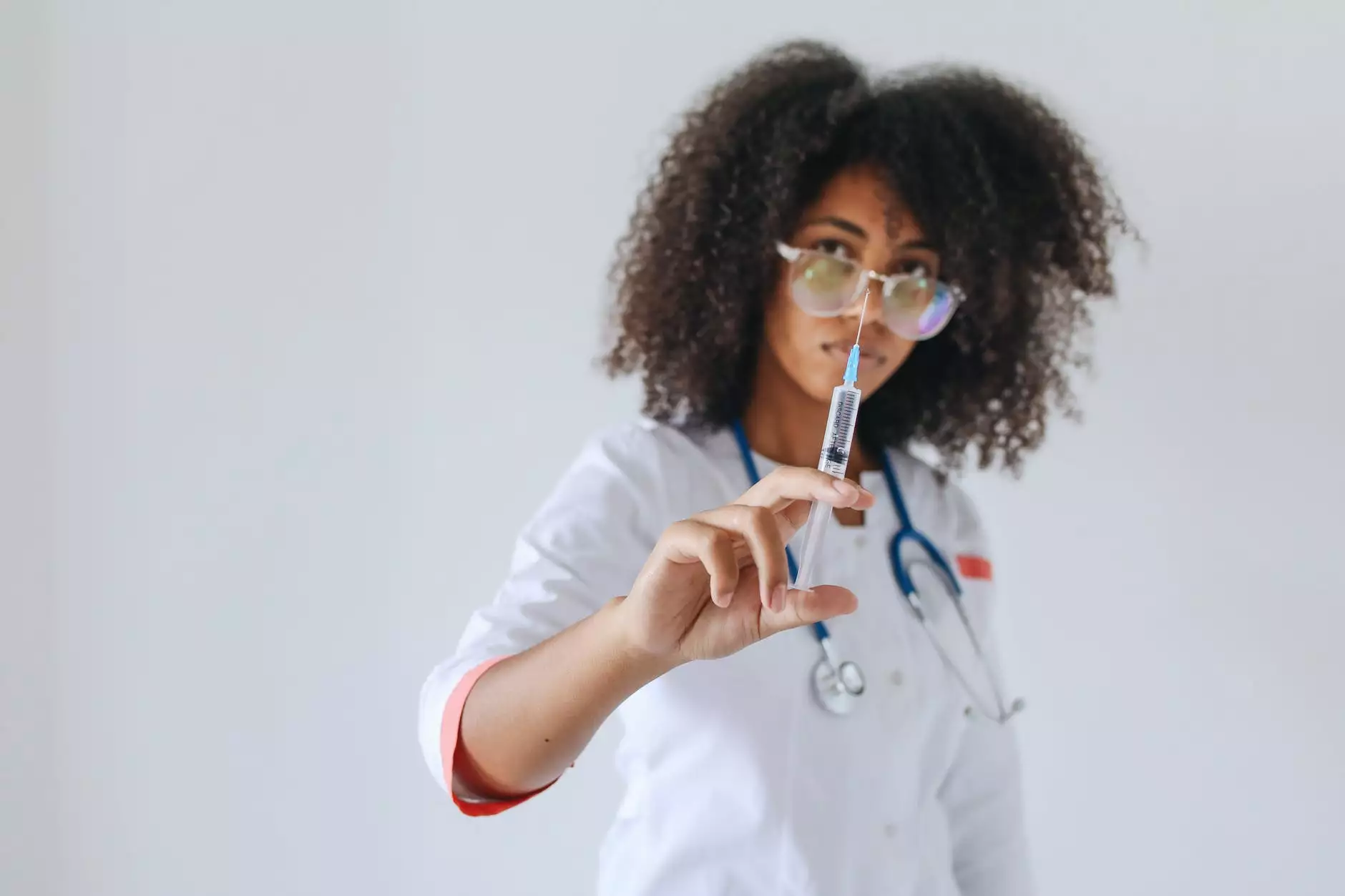
The plunger pump is a critical component in many industrial applications, renowned for its efficiency and effectiveness in fluid transfer. Understanding the plunger pump working principle can significantly benefit professionals in auto repair, farm equipment repair, and even within the realm of structural engineering. In this article, we will delve deep into the mechanics of plunger pumps, their applications, advantages, and how they are essential to thriving businesses like Michael Smith Engineers.
What is a Plunger Pump?
A plunger pump, often referred to as a reciprocating pump, uses a plunger to move fluid through a cylinder. It is characterized by positive displacement, which means it transfers a specific volume of fluid with each stroke, making it unique compared to other types of pumps. This feature is particularly beneficial in applications requiring high pressure and precise fluid delivery.
Key Components of a Plunger Pump
- Plunger: The main component that creates pressure and moves the fluid.
- Cylinder: Encases the plunger and provides a pathway for the fluid.
- Valves: Ensure one-way flow of fluid, typically including an inlet and outlet valve.
- Drive Mechanism: Converts rotational motion into linear motion, driving the plunger.
How Does a Plunger Pump Work?
To fully grasp the plunger pump working principle, let’s break down the process into manageable parts. The operation involves two primary strokes — the suction stroke and the discharge stroke.
Suction Stroke
During the suction stroke, the plunger moves backward within the cylinder, creating a vacuum that allows the inlet valve to open. This action draws fluid into the cylinder from the source. The design of the valves is crucial here; they prevent backflow, ensuring that no fluid escapes as the plunger retracts.
Discharge Stroke
As the plunger moves forward, it compresses the fluid within the cylinder, increasing its pressure. The pressure eventually rises enough to close the inlet valve and open the outlet valve. The fluid is then discharged out of the pump. This continuous cycle of suction and discharge allows for a reliable flow of fluid under high pressure, making plunger pumps ideal for heavy-duty applications.
Applications of Plunger Pumps
Plunger pumps are utilized across various sectors due to their robust design and dependability. Here are some common applications:
1. Auto Repair
In the auto repair industry, plunger pumps are indispensable for tasks such as fueling systems and hydraulic applications including brake systems. Their ability to maintain consistent pressure ensures that vehicles operate smoothly and efficiently.
2. Farm Equipment Repair
Farm equipment, especially those involved in irrigation and liquid fertilizer application, frequently employs plunger pumps. These pumps facilitate the precise application of liquids over large areas, enhancing farming efficiency and productivity.
3. Structural Engineering
In structural engineering, plunger pumps are utilized for concrete pumping and other construction applications where high pressure is required to move heavy materials. This capability allows contractors to achieve complex structures while ensuring material integrity.
Advantages of Plunger Pumps
The use of plunger pumps comes with several compelling advantages:
- High Pressure Capability: Plunger pumps can operate under high pressures, making them suitable for demanding industrial tasks.
- Accurate Flow Control: The positive displacement feature allows for precise control over fluid volumes, essential for various applications.
- Durability: Constructed with robust materials, plunger pumps are built to withstand harsh environments and heavy usage.
- Low Maintenance: Their design minimizes wear and tear, leading to lower maintenance costs and downtime.
Choosing the Right Plunger Pump
Selecting the appropriate plunger pump for your application is crucial. Factors to consider include:
1. Fluid Characteristics
Understand the properties of the fluid you will be pumping, including viscosity, temperature, and whether it is corrosive. This information will guide you in selecting a pump that can handle those specific conditions.
2. Pressure Requirements
Determine the operational pressure needed for your application. Plunger pumps can achieve varying pressure levels, and it’s essential to choose one that meets your demands without compromising efficiency.
3. Flow Rate
Evaluate the required flow rate for your system. Ensure that the pump can provide the necessary volume of fluid to maintain operations without interruption.
Maintenance Tips for Plunger Pumps
- Regular Inspections: Frequently check for signs of wear and tear on the plunger and cylinder.
- Monitor Fluid Quality: Ensure that the pumping fluid is filtered and free of contaminants to prevent damage.
- Lubrication: Regularly lubricate moving parts to minimize friction and wear.
- Seal Checks: Inspect seals for leaks or wear and replace them as necessary to maintain pressure integrity.
Conclusion
Understanding the plunger pump working principle is vital for professionals in various industries, from auto repair to farm equipment repair, and even structural engineering. The efficiency and reliability of plunger pumps enhance operational productivity and ensure that your business runs smoothly. By leveraging this knowledge, businesses can make informed decisions about the types of pumps that will best meet their specific needs and increase overall efficiency. At Michael Smith Engineers, we are committed to providing the best solutions for your pumping and engineering needs, ensuring your success in today’s competitive market.